Component Obsolescence: Is Your Process Up to the Challenge?
Component obsolescence: Is your process up to the challenge?
Electronic component obsolescence presents unique product design challenges such as continuity, quality, cost management, and support for the total life of the product. There are constraints on components and substitutions based on the original board design, customer requirements (e.g., cost, time, functional, environmental requirements), ability to match components for identical drop-in capability versus re-design or interposer modules to resize and allow for drop-in, impact of semiconductor die shrinks on functionality(e.g., noise susceptibility, drive capability, signal integrity, different edge rates, etc.), and supply issues for the immediate and life of the product time frames.
As a result, obsolescence or end of life (EOL) component challenges can prove to be critical events. Importantly, as an engineer, being able to design solutions that enable your products to perform to specifications and environmental requirements without an impact on the product quality, functionality, or otherwise for the customer is a real challenge.
Having components go EOL is a critical challenge to customers, but one that is often blind to them as it lands on your desk as a challenge to solve quickly and thoroughly. When EOL events occur, dedicated collaboration across the supply chain is essential to solve design challenges. Collaboration between end-product manufacturers, Original Component Manufacturers (OCMs), and component distributors, who can provide viable supply options for quality EOL components, is one important piece to the design challenge.
EOL events are not just about component supply though; obviously, the design challenges for maintaining end-products, particularly for board designs, are compounded during EOL events. At component EOL points, there are critical life-cycle design issues for engineers because board redesigns are not only costly but also time intensive, often require resubmission for recertification, and may also propagate into changing multiple components to maintain compatibility between devices. Finding the best engineering and business solutions to meet all of the needs during an EOL event and the forecasted life cycle of the board or end-product housing the EOL components often presents a complex decision point when all of the above challenges come together and well-thought through decisions must be made.
Adding to these EOL challenges is the threat of counterfeiters who regularly target the EOL sector. Not only are there (re-)design considerations during these EOL events, but there are critical sourcing and cost strategies that often necessitate including alternate supply sources due to lack of part availability through traditional channels. Collaboration with a trusted supplier offers options for managing the challenges of EOL, from providing a new channel of important information, to component life-cycle analysis, to authenticity and quality assurance.
The problem in a nutshell
Let's consider some of the design and related challenges faced by engineers when a Product Change Notice (PCN) is issued and components are flagged as a Last Time Buy (LTB) or have moved into an EOL stage. Very often components go obsolete and have a shorter life cycle than the products they are designed into. There are cases where some components have a very short life cycle and can actually go EOL before the product even gets released to production.
Many products in the industrial, aerospace, automobile, military, and similar markets must be supported for 5 to 20 years or even longer. Having a proactive, comprehensive, component obsolescence process is key to meeting product life cycle requirements, balancing the various business and design needs, and ensuring quality, EOL component procurement.
To help think about some of the less-considered issues around EOL component procurement, this discussion presents some of the actual process and decision flow-downs typically taken by an end-product manufacturer, OCM, and a component distributor. This view provides a wider perspective than what is typically considered by exploring the ecosystem of solution design for EOL component challenges while mitigating various risks, including counterfeit components which specifically target EOL component stages, and discrepancies between specification sheets and the actual form and/or functionality of the components. 1
1. “Component Obsolescence: Is your process up to the challenge? : Chelsea, Gibbs, & Cairns. 10 May 2013
Coping with the issue of obsolescence has become an increasingly difficult task, due to the ever- presence of substandard and counterfeit product present in today’s supply chain. Having a trusted, qualified, go-to independent distributor can mitigate the many risks associated with spurious obsolete product. Lintech has risen to the challenge of managing and obtaining obsolete and hard to find product and its associated issues. Monitoring end of life and providing our customers with critical information such as red-flag notice, product change alerts, and end of life notification provides our clients with a new channel of important information. Lintech’s dedicated procurement specialists are experts in sourcing obsolete and difficult to find product, and strive to acquire last time buys for customers who may have missed the opportunity. These products are then put through a stringent inspection and re-certification process. Our ISO 9001, AS9120, QMS-9090 and ESD S20.20 certified quality management systems help to insure product quality and authenticity, alleviating the pain associated with receiving counterfeit components.
Media Contact:
Shauna Ryan
Lintech Components
VP of Marketing
631-580-9500
ShaunaR@Lintechcomponents.com
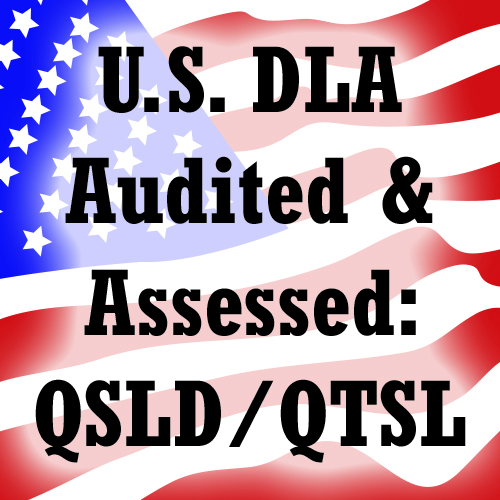
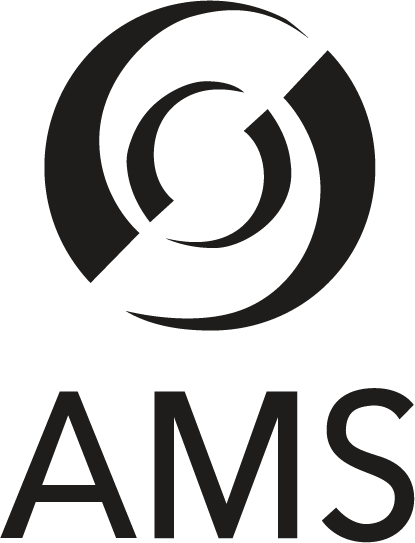
AS6081 Methods
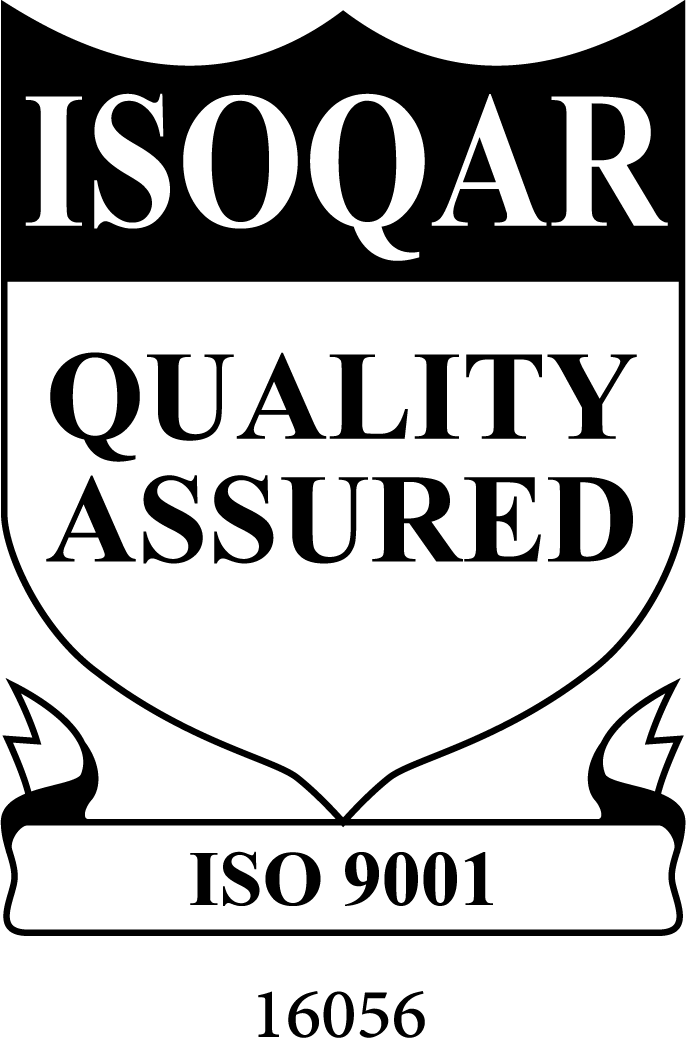
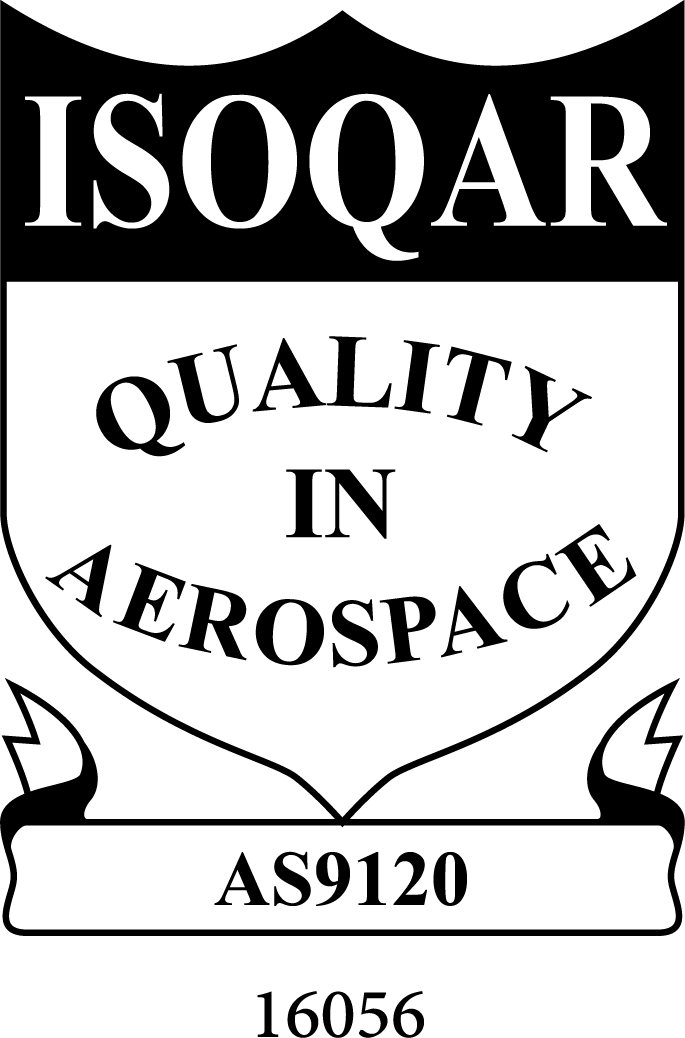
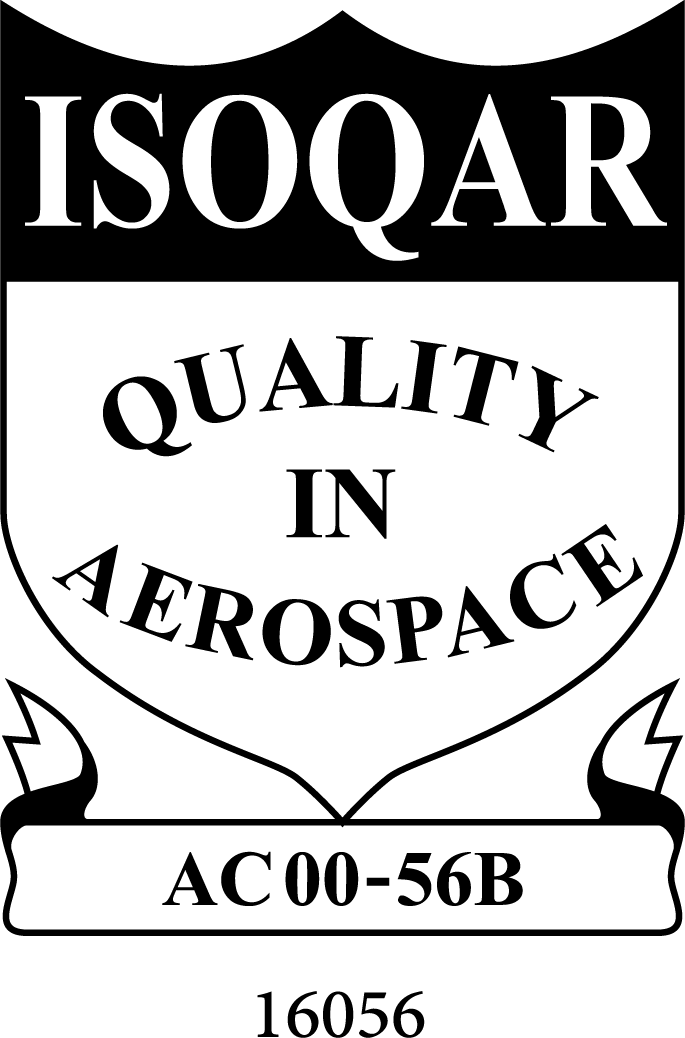
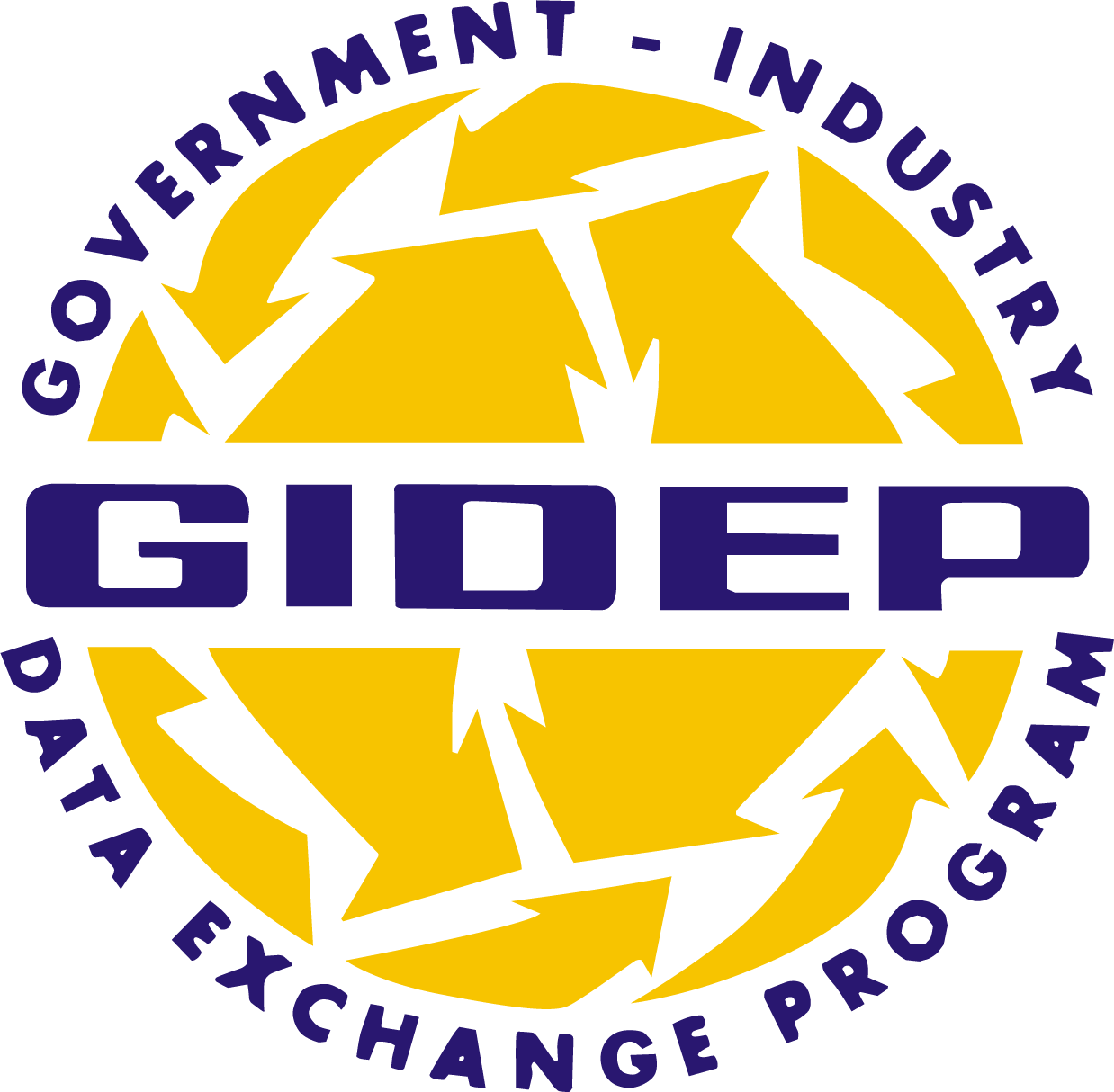